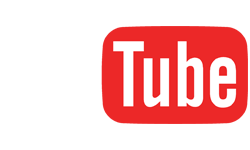
We hope to bring you new and interesting content on our YouTube channel. Please support us by subscribing.
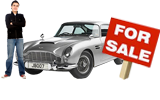
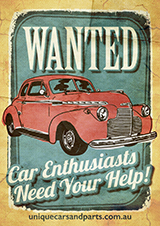
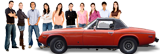
![]()
The first thing you will notice about any car is the colour and condition of its paintwork. While great looking duco makes your car look good, and is critical during re-sale, you should never overlook the fact that the most important function of paint is to protect the body against rust and deterioration caused by the action of the oxygen in the air, aggravated by acid and moist atmospheres. Modern car manufacturers recognise the need for body protection and go to great lengths to provide it. If the surface of a new vehicle could remain undamaged it would virtually last for ever; unfortunately, bumps and collisions, spatterings of grit and stones and flexings of the body all remove or crack the paintwork.
The bare metal is exposed and rust, the great enemy, creeps in, spreading under hitherto sound material. Production-line finish rust prevention starts at the steel mill, where newly-manufactured sheet steel is sprayed with oil. During transport to the car manufacturer's body-building line and during the pressing and welding of the many body parts, this film remains and is indeed augmented by additional sealants forced into seams, welding creams, drilling lubricants and similar materials used during assembly. Finally, the completed body shell - at this point a dirty, greasy object - is delivered to the paint shop. At The Paint ShopThe first task is to clean it thoroughly using white spirit and hot detergent pressure sprays. It is then vacuum cleaned to remove every particle of dust and grit, and immediately enters a tunnel on a moving conveyor. In this tunnel, several hundred feet long, paint application areas are interspersed with forced drying sections. The initial step is to provide basic protection by spraying phosphate etch over the entire body. This material bonds very securely to the metal surface and, when dried, has a slightly rough feel, ideal for keying on the subsequent paint coats. A paint dip, up to window level, into a bath of red oxide primer follows; after drying, this primer assumes a chocolate colour. Excess 'runs' are rubbed down and then two or three coats of zinc-rich primer are applied by automatic spray. High-Bake OvensBody sills and other enclosed areas receive applications by long-nosed spray guns, through designed-in apertures or holes drilled for the purpose. Each coat is dried and rubbed down, then further sealers are applied along all joints. Next, the under-body seal is sprayed on automatically and the shell is baked to 300°F (149°C) to dry off all traces of moisture. Two or three coats of acrylic lacquer follow, applied both by hand and automatic spray but with the last coat entirely by hand. The 'high-bake' ovens, operating at a temperature around 115°C (240°F), dry the lacquer coats quickly. Blemishes are removed and then the body is reheated to allow the lacquer to 're-flow' - in effect, this means that a layer of Liquid Perspex (Lucite in the USA) forms all over the surface to give a very tough, mirror-like finish. Finally, the interior voids of the sills are sprayed with a bituminous paint and the finished body is delivered to the assembly line. At every stage, rigid control of paint colour, temperature, viscosity and application pressures has been enforced. Specialist Repairs At The Body ShopAfter damage to a vehicle has been rectified, It is handed over to the spray shop to restore its original appearance. The panelbeater obviously cannot follow the exact methods of a production line since they may be dealing with ten different makes of car in ten different colours every day, each requiring only limited areas of paint renewal. The car may be received by the sprayer with perhaps a new door fitted, or with crumpled areas restored as far as possible. Their first job is to degrease the damaged or renewed areas. Fillers are then applied to bring 'low' patches up to the correct level. When dry, these are sanded down; one or more undercoats are applied followed by further sanding, then two or three finishing coats. Colour Matching, Viscosity and BakingThese finishing coats are carefully blended in with the existing paintwork, leaving the appearance of the vehicle as good as new. This may not sound too difficult, but the professional sprayer has to understand a wide range of materials, appliances and procedures. Some materials react adversely with others, so they must know which are compatible; they must understand colour matching, viscosity and baking, and the handling of their spray guns and other equipment. Many of these procedures can be done by the do-it-yourself car enthusiast - but practice makes perfect, so dont try anything until you have some experience under your belt. Materials Wax and Grease RemoversBefore any filling or painting is commenced, all metal surfaces must be completely free of oil, wax, grease and other residues. White spirit is widely used for this purpose, but there are many other specialised solvents and detergents. It is important not to touch a surface once it has been degreased otherwise 'finger grease' from the sweat glands of the skin will cause contamination and may spoil the adhesion of the paint coats. Paint removers: modem products will soften old paintwork of any type in 10 to 15 minutes and if can then be scraped off by hand. When stripping glass fibre bodies, the stripper must be removed from the surface after this time otherwise it may soften the basic material. Rust RemoverThis is an acidic preparation that not only removes rust, but also reacts chemically with the metal to prevent further rust formation. After application, any sludge formed around beadings and joints should be washed off with water and dried out with compressed air. Filling and priming should follow as soon as the surface is dry. Fillers, Sealers and StoppersThese materials are legion; there are hard-setting fillers that can be forced into joints and cured by heat; there are plastic sealers that will flex with parts of the body; there are rubber and resin-based fillers; there are fillers that can be brushed on, others that can be sprayed and others that can be applied by scraper knife. There are also combined primer/fillers which enable two operations to be performed in one action. Sanding - Wet and DryCommonly used grades of 'wet and dry' paper are 180 for the coarsest work, through 230, 280 and 320 for the undercoats, to 400 grade for the finest finish. Except for the coarsest grade, use the paper wet, using long, even strokes, not a circular motion which is almost certain to show through the final coats. Discard the paper before it becomes clogged. PrimersThere are primers available today to meet every need. Chromated primers for maximum corrosion resistance, self-etching primers, red oxide primers and others for use over rubbed down (or 'flatted') paintwork. Always check that the primer used is compatible with the finishing-coat material, otherwise bubbling, streaking or crazing of the final finish may result. ThinnersMost finishes (except aerosols) require thinning before application. Manufacturer's instructions must be followed implicitly in this respect, both as to the type of thinner used and the quantity required to produce the correct viscosity of the finishing paint. Finishes - Lacquers and EnamelsThe first automobiles were finished with ordinary oil-bound varnish colours, applied by hand but, from about 1920, nitro-cellulose lacquers, which could be sprayed on, came into general use with the development of mass production. High-bake cellulose enamels were developed about ten years later, and were widely adopted in post-war manufacturing plants. From about 1950 acrylic finishes made their appearance, at first mainly with metallic colours. The acrylic resins used in this material are better known under the trade name Perspex (Lucite). There are also several synthetic finishes, which do not contain either cellulose or acrylic materials. The main difference between lacquers and enamels is that lacquer dries out as its solvents evaporate, whereas enamels harden by chemical reaction. The drying of both lacquers and enamels can be speeded up by the application of heat and there are 'high-bake' and 'low-bake' examples of each available. High-bake paints are used on the body shell on the production line. But your local body shop cannot use these high temperatures on a completed car or the fittings and trim would be damaged, so they uses 'low-bake' finishes requiring a temperature of around 91-93°C (195-200°F)· As the result of stringent anti-pollution laws, especially in the USA, the discharge of harmful solvents into the atmosphere is very much restricted. Research in the 1970s developed methods of using safe solvents in what were known as non-aqueous dispersion (NAD), acrylics - and better still the elimination of all solvents, with paint being applied electrostatically in the form of a powder which is then heated until it flows into a high-gloss finish. Colour MatchingThe professional car-body sprayer must be able to match any standard vehicle colour exactly. Each decade there are over 4000 different colours employed by car manufacturers, and it is impossible for the sprayer to stock each one. Fortunately, the leading paint manufacturers have developed a computer controlled paint matching service to facilitate their task. Under the scheme, the paint manufacturer obtains a panel of each new colour from the car maker and its colour wave lengths are accurately recorded on a chart by a spectrophotometer. As a result, the sprayer need hold a stock of only about 40 standard colours from which they can accurately match any body colour, in any quantity, by reference to a printed guide, which gives the exact weight of each standard colour that is to be mixed. An accurate balance, therefore, forms an essential part of the scheme. For example, to prepare British Racing Green, specified weights of the standard colours White, Mid-chrome, Green-gold, Prussian Blue and Blue-Black are required. ViscosityThe viscosity of the paint at the moment of application is of the utmost importance and it must be known accurately if a satisfactory finish is to result. Viscosity is measured by timing the period taken by a given quantity of the paint to run through a funnel-shaped 'viscosity cup' at a specified ambient temperature. Except when applied by aerosol, the manufacturer's specified viscosity figure for the paint must always be attained, by the addition of thinners, before spraying commences. This figure is quoted in seconds, representing the 'run-out' time of the thinned paint through the viscosity cup. The effects of incorrect viscosity can be recognised as follows: Paint too thin - surface does not cover and paint 'runs' easily. Paint too thick - coverage is very restricted and paint forms 'blobs'. Spray GunsProfessional spray guns are operated by compressed air; their purpose is to atomise the paint into a spray and at the same time eject the spray on to the surface being painted. Account must be taken both of the pressure and the volume of the compressed-air supply. Gravity feed and suction guns with screwed-on containers are commonly used for small areas, but for larger jobs, pressure-feed guns are used; with these the paint is forced up from a container which may hold as much as 45 gallons. There are numerous types of air caps, fluid tips, fluid needles and spreader valves that can be fitted to the guns in order to cope efficiently with various viscosities, flow rates and spray patterns. The gun must always be held perpendicularly to the surface being sprayed, and each pass must be parallel to the surface (not swung in an arcj= this requires plenty of wrist action. Release the trigger at the end of each pass, otherwise the paint will build up at each end of the stroke and run. If the edges of the sprayed area are masked, start and finish each pass on the masking material. Before starting any job, test spray an area of any smooth surface such as a piece. of hardboard to optimise spray pressure and distance, and to check viscosity. It is usually more satisfactory to spray a complete panel - the whole of a door for example - rather than a small patch. Small differences in colour or texture are disguised if the sprayed area is taken to a natural join in the body. The correct distance to hold the spray gun from the work is about 8 inches; if held too close, the atomised mist reforms and the paint builds up quickly into a narrow area and runs or sags. If held too far away, the paint droplets are spread out too much and cannot join together. As a result, the undercoat shows through. In addition, if the gun is held. too far away, a dusty or sandy finish may result due to excessive volatilisation of the thinners between the gun and the sprayed surface. Spray pressure should be set according to the paint manufacturer's recommendations, and may vary between 40-80 lb per sq in (2.8-5.6 kg per sq cm); the finishing coats usually require the higher pressures. After use, if the same colour will be required again soon, it is sufficient to remove and securely cover the reservoir of the gravity or suction-feed gun. To clean a gun, which should be done as soon as spraying is finished, pass thinners through the gun instead of paint. Wipe the exterior with solvent-soaked rag. For the d-i-y car enthusiast, for whom a 'compressed-air supply is not usually available, the choice lies between the aerosol spray and the electrically operated spray gun. The above notes on the use of the spray gun should be followed where applicable. Brush PaintingAlthough a brush-painted job cannot really compete with a good spray finish, nevertheless circumstances may sometimes favour brush application, for which special quick-drying cellulose undercoats and lacquers are available. Large areas are the most difficult. For example, a roof, where each stretch, as it is painted, must be joined up to the next before the paint gets too dry. Fast working is therefore called for, with just the right amount on the brush - enough to cover in one pass, but not enough to run. Do not attempt to paint in sunshine, that is, while the metal is hot. Here again, practise on a piece of smooth material first. After a drying period of at least 48 hours, a fine cutting or finishing compound will produce a good polish. The compound, thinned to a creamy paste with water, is applied evenly with a damp cloth. Take care not to rub through edges or swage lines. Rinse off with clean water and wipe dry. BakingTo speed production in the paint-spraying shop, movable booths, drying arches or panels are available. These usually consist of a battery of infra-red lamps and are adequate to provide the low-bake temperatures required. Baking time is usually around 40 minutes. Cleanliness and SafetyFor good results, the atmosphere must be dry and dust free. This is recognised by the professional, but the amateur sometimes does not take into account how easily dust can be stirred up merely by walking over a concrete garage floor, how much lint can drop from a pair of cotton overalls or an old pullover, or how much dust can fall from rafters. It is good practice to remove old-rags and sacks from the working vicinity, to wash down and dry the garage floor before starting, and to wear nylon overalls while spraying. If possible, support a large polythene sheet over the vehicle, and do the job on a sunny, windless day. The inhalation of solvents and' atomised paint is obviously undesirable and ventilation must be provided. An industrial mask covering nose and mouth should always be worn while spraying. Remember that new paint can take several weeks to harden fully. Care of PaintworkMost modern finishes require no more than being kept clean by washing: the application of polishes can often do more harm than good. If in doubt, consult the vehicle manufacturer. If the paintwork is damaged, the most important immediate action is to cover any bare metal with paint - an aerosol spray is useful for this job-before rusting can take place. Rectification of the damage can be left until later. Another often unrecognised source of damage to the paintwork arises from covering the car with tarpaulin or plastic sheeting. This is very bad practice and can cause considerable damage from the sheet flapping in the wind and grinding dirt into the paint surface. In addition, condensation forms under the sheet which is unable to dry out. It is far better to leave the car open to the atmosphere if it cannot be garaged. In fact, the only time we at Unique Cars and Parts use a car cover is when storing a car in a garage, out of the wind and rain, so that it is effectively only a "dust cover". Also see: Rust - The Enemy of Every Car | Color and Paint Codes by Manufacturer and Year
|