The
internal combustion engine is a direct descendant of the reciprocating steam engine. Otto and other pioneers adapted many ideas from the steam engines of their time. This created internal combustion problems right from the start, because the old reciprocating steam engine was essentially a low-speed device, while the
internal combustion engine needs speed to get its power. But you shouldn’t sell these early pioneers short, though, because many ideas we consider up-to-date were first developed in the very early days of
combustion engines.
Overhead valves and hemispherical chambers are two such examples. The earlier developers were limited by materials and machine tools, so they made compromises. These factors caused a slow evolutionary development over a period of many, many years. Things started to change rapidly in the 1960s because the pace of development and change in combustion chamber design had been going on at a furious rate – particularly given the emphasis on performance, coupled with tough competition in the auto industry.
Residence Time of the End Gas
A quick review of combustion theory will help you visualize the various chamber layouts. Combustion occurs in four phases: the pre-flame reaction, the cool flame front, the blue flame front, and finally the undesirable auto-ignition. Auto-ignition is what causes detonation and induces pre-ignition - and these are the engine busters. Since it's the last part of the burning charge that's likely to detonate, you can see how important it is to get the charge burned quickly (before auto-ignition of the end gas - or last part of the unburned charge - has time to take place).
In other words, the longer the last part of the charge remains unburned in the cylinder, the more likely you are to get auto-ignition. Engineers call the time the last part of the charge stays in the cylinder the "residence time of the end gas." And this is fundamental to chamber design. Burning a charge too rapidly can also be a problem, because this makes for engine roughness. So the trick is to get smooth, even combustion and still get the blue flame front to move across the chamber before the end gas can auto-ignite.
The T-Head
Burning time isn't the only consideration; compression ratio, rpm, charge temperature, turbulence, type of petrol used, and fuel/air ratio all have an important influence on engine combustion. Dependability of the early engines was a big problem. It limited the widespread acceptance of automobiles. So it's natural enough that reliability and accessibility became overriding factors in all phases of early automotive design. This, along with low cost, dictated the T-head configuration. This head gave low performance, poor volumetric efficiency, and had poor knock characteristics. But it was reliable, because it was accessible and rugged. Almost no consideration was given correct spark plug location, because no one really knew where the best plug locations were. Knocking was an accepted fact in those days, but then you always had the spark lever to remedy the situation.
The L-Head and F-Head
As more cars were sold, more money became available for research and development. We began to see a great variety of designs in general use. For example, L-head and F-head came into wide commercial acceptance, while overhead and hemispherical layouts started turning up more often, especially in racing circles. Incidentally, one of Otto's early engines had a hemispherical chamber, but it was too expensive and hard to make. Much of the credit for the modern developments we have today should go to the metallurgical engineers. Right through until the early 1960s all the engine designers did was dust off the old designs and build them with modern materials and machine tools. The superior performance of overhead-valve layouts and hemispherical chambers was attributed entirely to better breathing and not to better combustion. Also, since compression ratios were low, auto-ignition, although often present, was no serious problem. As engineers tried to raise compression ratios to gain efficiency and specific performance, auto-ignition became acute.
The Knock Barrier
The auto industry had now reached the knock barrier. Harry Ricardo broke this when he came up with a plausible theory of combustion. Once Ricardo analysed combustion correctly - it was simple to come up with geometric configurations that could eliminate the knock problem. Ricardo's combustion chamber was the first to utilize a "squish area" to gain turbulence and keep the end gases cool. Incidentally, fuels were also modified at about the same time. They included additives to make them more knock resistant. Ricardo's ideas were quickly adapted to L-head and F-head designs. This let designers raise their compression ratios, thus giving new life to these designs. L-head and F-head layouts had drawbacks from a volumetric-efficiency standpoint, but they were cheap to manufacture; consequently, they had a very long and prosperous life in the auto industry. Here are some of the precepts of chamber design that Ricardo formulated, based on his findings about combustion:
Increase Turbulence
Rule #1 - Increase turbulence in the burning charges. Turbulence increases the flame speed in a charge and greatly aids in completing the burning process before the end gas can auto-ignite. Ricardo implemented this theory by introducing a squish area (see Figure 6). As the piston reaches tdc, very little clearance (less than 1/16-inch) is left between the head and piston. This causes the gases originally occupying this area to be "squished" out. The squished gases are sent into the main chamber area with great velocity. This results in mixing and turbulence and greatly reduces residence time and the tendency toward auto-ignition. Pistons can also be modified to add to the turbulence. If either of these two methods (squish area or contoured pistons) is used to put turbulence in the charge, it's called "compression turbulence."
This type of turbulence has several distinct advantages: First, by blanking off some of the effective piston area, the rest of the cylinder becomes very compact. Second, there's no drop in volumetric efficiency, because all the turbulence starts after a full charge has been taken into the cylinder. Turbulence can also be induced by careful layout or "biasing" inlet ports, inlet valves, or inlet manifolds. This is known as "induced turbulence" and is quite common in ohv engines. Examples of induced turbulence would be machined sleeves in the intake ports or cast protrusions in the head. Induced turbulence causes some drop in volumetric efficiency, especially at high rpm, because this approach involves some restriction to flow and also disturbs smooth flow. Don't make the mistake of thinking that turbulence in a combustion chamber is a panacea - it can make for too rapid combustion, and that results in engine roughness. The pressure rise rate limit for smooth combustion is normally less than 30 psi per degree of crank travel. Anything above this value tends to lead to surface ignition, rumble, or roughness.
Small Combustion Chambers and Spark Plug Location
Rule #2 - Make combustion chambers as compact as feasible. This, of course, results in shorter flame travel and gets combustion over in a hurry. In other words, burn the charge quickly before it gets a chance to auto-ignite. A secondary benefit is that less heat's lost to the cooling jacket. Rule #3 -
Put the spark plug near the hottest part of the combustion chamber. The hottest point in a chamber is the
exhaust valve. Since the charge in this area is very susceptible to auto-ignition, burn it first so it doesn't have time to auto-ignite. Rule #4 - Locate the spark plug as near the center of chamber as possible. This trick would tend to cut in half the distance a flame front would have to travel, thereby cutting burning time in half and not giving auto-ignition time to take place in the end gas. The squish technique had another advantage. Since the small volume of gas trapped in the squish area was exposed to a large surface area of the engine, the tendency was to keep this end gas cool enough to avoid auto-ignition.
Overhead Valves and Wedge Chambers
It wasn’t all that long until the auto industry passed the L-head, F-head era and moved into overhead valves. The idea is to make the overhead valves as large as possible to increase volumetric efficiency, but you reach a size limit if all valves are in the same plane. This is one disadvantage of wedge chambers that's not shared by hemispherical chambers. Hemispherical chambers are superior to other chamber layouts, because they adhere more closely to Ricardo's principles. But the high cost and valve complexity of hemispherical layouts severely limit their wide acceptance. In general, the industry turned to a chamber layout that kept many of the advantages of the hemispherical layout, yet at a greatly reduced cost. This compromise layout was the wedge chamber.
Wedge chambers are often designed to have both "induced" and "compression" turbulence. They're also very compact and, in general, easy to manufacture. Although there are various possible spark plug locations in a wedge chamber, it's the general consensus that putting the plugs at or near the corner of the wedge gives the smoothest combustion. Combustion in a wedge chamber starts slowly, burns quickly during the middle phase, and slows down at the end of the burning cycle. In other words, wedge chambers don't shock-load the piston with burning gases.
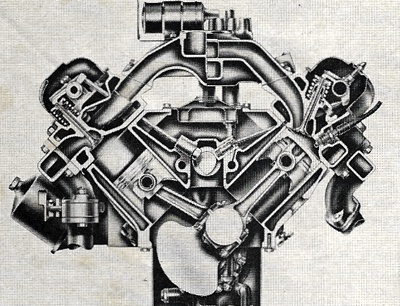
Dodges polyspherical chamber put the valves in one plane, thereby keeping the Hemi's good points while reducing cost in manufacture.
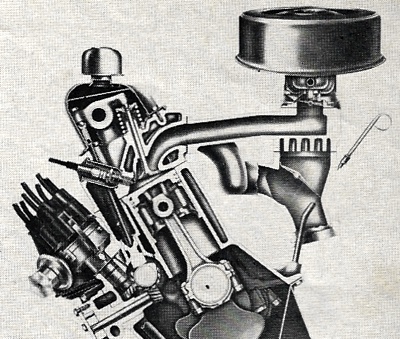
A Chrysler Wedge Head cutaway of the 225 Slant Six.
A High Performance Chrysler Hemi-Head V8, which used domed pistons to raise compression. The plugs stood at the centre of the dome.

Chevy's Flat Head engine, where contoured pistons give a wedge shape. This cut manufacturing costs, while providing a large squish area.

The Corvair's combustion chamber was a modified wedge formed entirely by the cylinder head. There was a relatively large squish area and increased finning near the chamber. |
Hemispherical Chambers
Ask any Valiant aficionado and he will gladly explain that hemispherical chambers have the best anti-knock characteristics and best volumetric efficiency, can rev to high rpm (due to light valve gear), but are expensive to build, and the valve gear is hard to maintain. Wedge chambers show extremely smooth combustion, have good turbulence and good volumetric efficiency. They're relatively inexpensive to manufacture, lightweight, compact, easy to maintain, and allow
cooling system capacity to be reduced. Building a combustion chamber so it has excellent anti-knock characteristics is called "giving an engine mechanical octanes." In other words, through careful adherence to design features, a combustion chamber can be built that's extremely knock-resistant.
This provided the engine designer with two choices. They could run a good chamber design on a lower-octane fuel or could raise the compression ratio provided there was a good design and still run on a fuel that would normally be unacceptable with a poor design. Below is a list of rules formulated on combustion research since Ricardo's time.
a) Design the combustion chamber (including the location of the spark plug) so that high compression ratios can be used without increasing the octane requirements of the fuel (mechanical octanes). In other worlds, rapid and complete combustion are musts.
b) Good volumetric efficiency means maximum air consumption in modern engine designs. In addition to combustion chamber design, valve timing, valve size, streamlined intakes and exhausts, low pressure losses through carburetor Venturis, tuned intakes and exhausts — all these have important effects on volumetric efficiency. In regard to combustion chamber design, we can increase volumetric efficiency by minimizing the contact between the incoming charge and hot spot in the chamber. Overheating the incoming charge expands the charge and thereby reduces the amount of charge that can be taken in. Engine deposits can also hurt volumetric efficiency. Still, evaporation of the fuel can help volumetric efficiency, because evaporating the fuel causes the temperature of the entire charge to drop. For example, if you use alcohol, it'll drop the temperature of the inducted charge four times as much as gasoline.
c) Keep the ratio of surface-to-volume of a combustion chamber small to minimize heat losses, increase thermal efficiency, and minimize "deposit depreciation" losses. "Deposit depreciation" loss might be new to you, so let's explain it a little further. Let's say we build a combustion chamber and test it thoroughly to see how it performs. In the tests, let's say the engine needs 90-octane gasoline to stay out of detonation. So far, so good.
d) Keep combustion-pressure rise rates as low as feasible to avoid shock-loading the pistons and avoid engine roughness. Normal limits are under 30 psi per crank degree and preferably between 20-25 psi per degree.
e) Eliminate all sharp edges and burrs from chambers (and plugs) that run at high compression ratios, because they tend to get very hot and can cause pre-ignition. Also avoid having gaskets protrude into cylinders.
f) Keep cylinder capacity of each cylinder in a multiple-cylinder engine as nearly equal in volume as possible.
g) Turbulence, both induced and compression, has been already covered. Suffice it to say this is being perfected.
h) Chamber design must not have pockets for burned, stagnant gases to collect in. This would result in rough idling and lower power outputs.
i) Last but probably most important, a combustion chamber design has to be as easy to manufacture as possible.
But engineers also faced another problem. After about 15,000 miles of the combustion chambers tended to have a layer of carbon and other deposits on them. These deposits did two things to a combustion chamber. First, they took up space so they increased the compression ratio. Second, they sometimes got red hot and caused pre-ignition. So now the engine would knock on 90-octane petrol, forcing the owner to switch to a higher octane fuel. This was known as deposit depreciation loss. It could be significant (5-10 octane numbers), so engineers normally designed with this in mind.
If you want to make a study of combustion chambers and how they change and evolve, Chrysler makes a good subject. They pioneered in mass-produced hemisphericals in
1951. Its reliability, durability, specific performance, and ability to withstand extreme performance modifications are well known, so it's no use to belabor this point. But cost was always a problem, so Chrysler tried various modifications of this chamber. One was the Super Red Ram V8. introduced in
1955. This engine featured what Chrysler called the Poly-spherical Combustion Chamber.
The hemisphericals were then dropped for wedges, such as the
1965 225-cubic-inch Six. But performance sold cars and created images highly desirable to any company wanting to increase market penetration. So you guessed it - back came the hemisphericals for the big 426-inch maximum-performance engines in
1965. This time Chrysler's pistons were highly domed to bring the compression ratio up as high as possible and put their cars as far out in front in the racing events as possible. Engines like this had combustion chambers that had a strong resemblance to all-out racing engines.
Internal Combusion Engine Definitions:
Compression turbulence — agitation and mixing of the combustible charge in a reciprocating engine during the compression stroke. Squish areas, domed pistons, or baffled pistons can be used to create this type of turbulence.
Deposit depreciation loss — new engines are carefully tested at the factory for octane requirements. As the engines are used, they build up deposits that can raise the compression ratio and cause undesirable effects in engine combustion. This could mean that the engine needs a higher-octane gasoline to run satisfactorily. The increased octane need is called "deposit depreciation loss."
End gas — the last portion of a combustible charge in a cylinder to be burned. Auto-ignition always originates in the end gas, because it's exposed to the highest temperatures and pressures for the longest time.
Induced turbulence — turbulence imparted to the incoming fuel/air mixture by angling the intakes, casting protrusions into the intake manifold, or by masking valves ... a very common method of getting charge turbulence in modern engines.
Mechanical octanes — an expression used to describe a combustion chamber whose combustion characteristics are so good that lower-octane gas can be used. In other words, actually building knock resistance into the combustion chamber.
Residence time of the end gas —the time from charge ignition (spark across the gap) until all the combustible charge is burned by the flame front. If the residence time is too long, auto-ignition results; if too short, rough combustion results.
Squish area — the space between the
cylinder head and piston at its closest point (usually less than 1/16-inch). Gas caught in the squish area is rapidly forced out across the combustion chamber, creating turbulence and cutting down burning time.